
How Glass Production Impacted Modern Architecture
How the Production Methods Changed
During the 1860's Henry Bessemer invented the float glass method of producing plate glass, which changed the way that we as architects use glass as a material. Before Bessemer, all of the glass was hand blown and this would take a while to do, but after Bessemer's invention though his method was still unsuccessful at being mass produced increased the amount of glass that could be produced as well as the size that could be obtained and decreased the time that it took

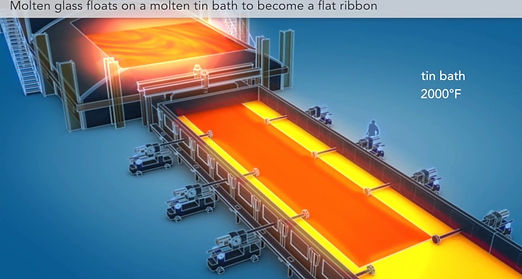
What Is The Float Glass Process
The Float Glass method invented by Bessemer in the 1860' was a new innovative way of creating sheet glass that would be exact and the same size though out the entire sheet of glass. This method of making glass is still in use today.
​
1) Melting and Refining
The process begins with mixing all of the fine grained ingredient of glass. Then after all the indigence are mixed together then is moved into a really hot oven that is about 1,500 degrees Celsius. During this process the materials are begin mixed while still melting. This melting process is the most important part to producing the quality glass.
​
2) Float Bath
In the second phase of the float glass process the melted glass is released from the oven and flows over refractory spout on to the mirror like surface of molten tin, that is roughly 1,100 degrees Celsius. When it leaves the tin bath the glass is a solid ribbon and goes through the rollers that are set to a specified thickness of the glass.
​
3) Coating
The third phase of this process is coating, though this part of the process may not have been apart of Pilkington's original thoughts behind the process. Now this part of the process allows us to chemically alter and enhance the material.
​
4) Annealing
The Fourth phase of the float glass process is annealing. The glass as it cools is under a large amount of stress. If the glass is under too much stress it will break when it gets cut. To relieve the stress that is on the glass it goes through a heat treat in a long furnace known as a lehr. While in this heat treat process the glass is closely monitored. Pilkington developed the technology that automatically feeds back stress levels in the glass to control the temperatures in the lehr.
​
5) Inspection
The fifth phase of the float glass process is the inspection. This part of the process is to insure and to clean up a few mistakes that the machines might have made during the process of making the glass
​
6) Cutting to order
The final phase of the process is to cut it to the specified size. Diamond wheel trims off selvedege, stressed edges, and then cuts the plate glass to the predetermined size.
​
​
​

How This Change in Production Methods Influenced Modern Architecture
Simultaneously with the changing in production methods, the modernist styles in architecture were starting to arise, as well as the theories behind it. The change on the production methods didn't neccessarily change how architects use the material, but it did make it possible for more glass to be used in buildings at a larger scale.